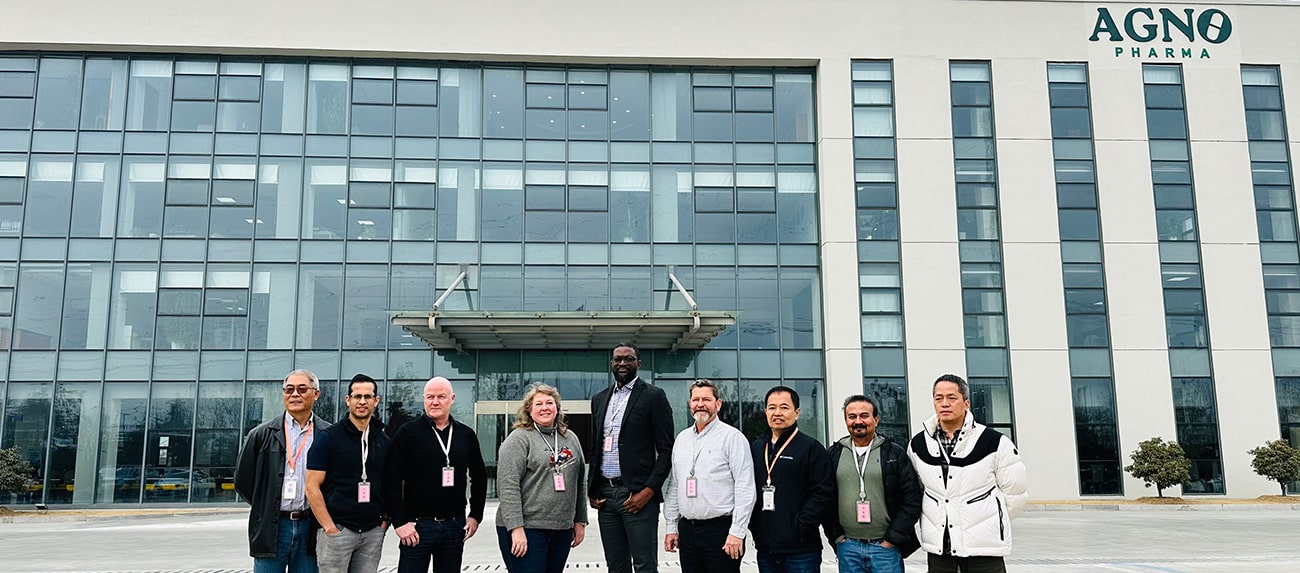
Behind the Scenes: Agno Pharmaceuticals’ Visit to Our State-of-the-Art Biotech Manufacturing Facilities in China
Table of Contents
An interview with:
- Shamim Ahmed, Ph.D., EVP, Pharmaceutical Development
- Mithilesh Deshpande, Ph.D., Director, Formulation Development
- Michael Mrvos, SVP, Business Development
- Jane Meyer, VP, Business Development
- Bruno Cuypers, VP, Business Development
- Onajite Okoh, Director, Drug Implant Development
Firsthand Experience at Our Biotech Manufacturing Facility in China
In January this year, several members of our U.S. team traveled to Agno’s two China facilities in Lianyungang and Suzhou to see the facilities firsthand and facilitate team building. This visit was transformative for our team and our understanding of all that Agno is capable of producing for our clients. Read about their experiences, insights, and takeaways below.
The Agno team was impressed from the moment they set foot in our China facilities. Both the Lianyungang and Suzhou sites exceeded expectations, which were admittedly high going in. The facilities are state-of-the-art by every standard, with the equipment and capabilities to support our clients’ complex and varied needs. What did the Team members think about the sites?
Jane Meyer: Regarding the Suzhou site, it was larger than we could fully appreciate from the U.S. Being able to be there ourselves and walk through the site allowed us to grasp its size and capabilities. One impressive aspect of the site was how many reactors at different scales were available, which means a client could go from milligrams to metric tons with all the equipment, analytical, and scalability.
It was clear the sites carried a pride of ownership. Every team member there was passionate about their work, and that came through in their pursuit of excellence at every stage.
Michael Mrvos: I was excited to see the expansion of new buildings with equipment and capabilities to support Beta-lactam sterile injectable commercial manufacturing. It was amazing to see the aseptic pilot fill line and the oral dose pilot suite.
Upon arriving at the facilities, our team was struck by the commitment to excellence in every aspect of building design, organization, and cleanliness. The facility in Lianyungang sits on 27 acres, with an additional 12 acres allotted for future expansion. The greenfield ability allows for incredible potential.
Mithilesh Deshpande, Ph.D.: I was completely overwhelmed when we visited the Suzhou site. The API facility, R&D, and manufacturing were state-of-the-art. The entire operation was well-segregated and well-managed. They’ve built up a state-of-the-art plan for drug product manufacturing, including modern aseptic processing design and automation throughout the facility.
A Look Inside: State-of-the-Art Facilities and Cutting-Edge Biotech Technology
The Agno team agreed that the sites boasted modern infrastructure, advanced labs, and high-tech equipment that empowers us to facilitate client success.
We asked our team to describe the facility in terms of its design and technology:
Onajite Okoh: Both facilities appear to be designed with growth in mind. Both sites have advanced labs that feed into manufacturing, which could offer potential clients a one-stop shop option.
Shamim Ahmed, Ph.D.: I’ve worked in this industry for over 30 years. When I worked on the client side, I easily visited over 100 CDMOs. The Suzhou facility is one of the best. It’s beyond imagination. If you don’t see it, you won’t believe it.
Many development companies can handle manufacturing, but not many can do compounding and filling in isolator systems, and there are few, if any, sites that connect sterile micronization with finished product compounding. These facilities are capable of all these components. After visiting this site, I feel very comfortable sending any client—from the U.S. or globally—there to manufacture their product.
Michael Mrvos: The facilities are very well designed in that R&D and small-scale intermediate, RSM, and API are developed and manufactured at our Suzhou facility and then scaled up to our site in Lianyungang, which has mega-ton-scale capabilities to support commercial products. We have new state-of-the-art equipment for the aseptic pilot fill line and the oral dose pilot suite, including new sterile API & DP manufacturing and packaging.
The sites had impressive quality control standards, having had six successful FDA audits since 2014, as well as monitoring and qualification of the cGMP facilities and equipment EQ, IQ, OQ, PQ, and current ISO requirements for environmental controls of the clean rooms.
Mithilesh Deshpande, Ph.D.: The sites boasted adaptable workspaces to meet changing manufacturing needs. We saw many automated systems, especially in terms of filling needs. Sterile manufacturing and aseptic processing present significant challenges. Agno has the capability of not only handling API but also sterile micronization, sterile drug product manufacturing, automated filling, stoppering, and labeling. Everything is automated with limited human intervention to ensure it’s all sterile.
Jane Meyer: The facilities are organized in a pod setup with isolated labs and analytical equipment. This allows for a focused effort team that can collectively work on products in a specific area, allowing for isolation and a team effect, which is a unique way to interplay for our clients.
There’s also a continual hydrogenation, multiple units, in the lab setting that can do scale-up, which I’ve never seen in any of the companies I’ve worked for. The sites allow for unique setups and scale-up capabilities, which were truly impressive.
The People Behind the Process and Culture: Hospitality & Expertise
In addition to seeing the facilities and experiencing all these sites had to offer, a primary goal of our visit was to build relationships with our colleagues at these facilities. The U.S. team was blown away at the hospitality they received from the beginning of the trip to the end.
Onajite Okoh: Everyone we met was intellectually generous and willing to teach or share information on how the processes were executed. Our colleagues at each site were very welcoming and accommodating. It was evident that this level of hospitality was organic and would extend not only to colleagues but also to clients and customers.
The team agreed that professionalism, dedication to their work, and a strong work ethic were foundational to the culture of the facilities. Our colleagues take pride in their work and are extremely flexible in this rapidly changing environment. They’re eager to learn and open to change, which has allowed them to evolve and grow over the years from a primarily API company to now delivering finished products. Innovation is at the heart of the people at our China sites, and Agno Pharmaceuticals and all our clients benefit from it.
The Impact on Client Projects: How This Facility Drives Success
Everything about the China facilities is designed to support and ensure client success. Access to the most advanced, modern technology empowers Agno to ensure efficiency, quality, and scalability at every stage for our clients.
Bruno Cuypers: The optimized design of these facilities allows for a smooth manufacturing process with all controls in place to document critical parameters from start to end.
Michael Mrvos: A few years ago, our team received an Intermediate for a clinical trial that cost $45,000/Kg to manufacture. Our team redeveloped the process to become more efficient, reducing the cost to $2500/Kg. The client received FDA approval, and Agno is now manufacturing the commercial supply. All of this is possible because of the innovations at our facilities.
Jane Meyer: These facilities provide by-the-hour turnaround information for customers, not weeks or longer, impacting the project’s success. By being highly reactive to the client’s needs and prioritizing responsiveness, you’re positioning yourself to be able to accomplish things that you usually wouldn’t because you took too long to get there.
Key Takeaways
After our team’s visit to the China facilities, everyone walked away with added confidence in Agno’s cGMP capabilities to support our clients’ projects from clinical development to commercial.
Jane Meyer: As all the pieces come together, you can see how everything from a small project to a large production can easily fit into the site, and you don’t feel it’s lost in the shuffle. In other CDMO facilities, some resources are so overshared between teams that you lose the presence of the project getting done on time or on budget. By having this focused effort as projects come in and ensuring those teams are designed around it, you can see how easy it is to achieve success in these projects.
Shamim Ahmed, Ph.D.: Today’s drug manufacturing clients want to hit three primary KPIs: cost, quality, and speed. Our visit to these facilities has given us confidence that Agno can deliver all three to our clients. Every building, every piece of equipment, every factor is state-of-the-art. No manufacturing or development facility can rival what we saw in China. Agno can execute client projects faster, at lower cost, and better than anyone else, thanks to the remarkable innovation of our Chinese colleagues and the work they’re doing in Lianyungang and Suzhou.
To wrap up, the Agno Pharmaceutical team would like to thank our Chinese colleagues for hosting us and showing us what can be done when expertise, state-of-the art equipment and capabilities, and 100 percent team buy-in come together. The things we’ve learned and seen, as well as the people we met with and learned from, will help us better serve potential and existing clients as they pursue drug development.