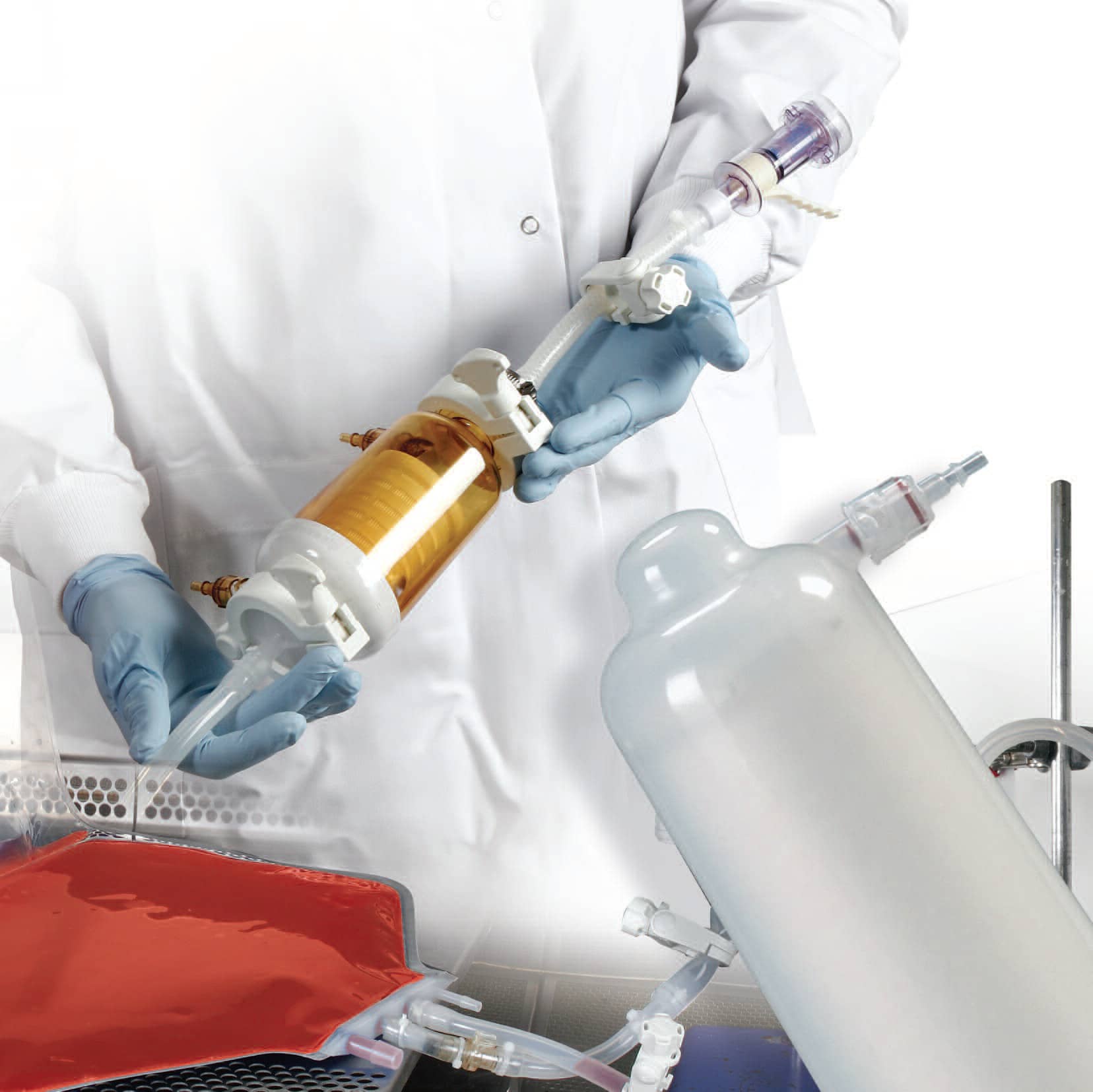
Phase Appropriate Filter Validation for Sterile Drug Product Manufacturing
Table of Contents
This post is the second part of a series on Filter Validation for Sterile Drug Product Manufacturing. Our first post focused on the key elements of filter validation. In this post, we will explore how filter validation testing evolves throughout clinical and commercial manufacturing. We will also explore how to avoid costly, time-consuming errors during the validation process.
When Should Filter Validation Testing be Performed?
Although regulations require that filter validation studies be performed for sterile filtration processing, there is no specific requirement for when the studies should occur. While manufacturers would prefer to conduct validation without regard to the practical limitations of early-stage product development, the realities of bringing a product to market require that they take a risk-based approach in deciding the appropriate time for validation. Early in the development process, there may simply be limited amounts of the product available or the final formulation may not yet be determined. If validation is completed at this time and changes to the formulation are made later, it may require revalidation, which is costly and time-consuming.
Risk-Based Phase Appropriate Filter Validation
Early Development
At Particle Sciences, we have incorporated a risk-based, phased approach to filter validation which focuses on three specific areas for early development projects: Compatibility, retention, and filter integrity testing.
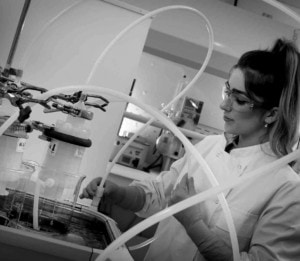
Compatibility
Filter manufacturers provide technical information on what the filter should be capable of and whether it is suited to a given process or type of material. In addition to gathering that information, reviewing compatibility charts, past literature and other sources can all offer guidance as to whether a filter is likely to be compatible with your product.
Chemical compatibility testing is used to determine the effect of the liquid on the filter and the effect of the filter on the liquid. Most filter manufacturers perform chemical compatibility testing on their filters over a period of seven days, after which the filter elements are checked for performance and integrity. It is important to check that your drug product is compatible with the filter early in the process to make sure the filter doesn’t negatively impact the quality attributes of the product.
Filter Integrity Testing
It is also important that integrity testing be conducted after filtration to detect any filter leaks or perforations that might have occurred during filtration. Initial filter efficacy studies will provide information regarding the filterability of your product and help to generate the necessary product-specific filter integrity specification for the bacterial retention studies.
Retention
The purpose of a sterilizing-grade filter is to remove microorganisms that may be in the solution. In order to show the sterilizing-grade filter is suitable, a challenge test is completed where your product is inoculated with an organism and then shown to be free of that organism after filtration. The physical characteristics of your product (such as pH or viscosity) and the filtration process (such as temperature, flow, or pressure) may impact the evaluation of the bacterial retention of sterilizing-grade filters.
Commercialization
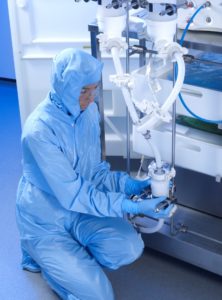
During later phases of development, as you are preparing to submit your marketing application, filter validation activities focus on the other five aspects included above. At this point in development, the production design space will be sufficiently developed so that the more costly tests such as extractable/leachable studies may be completed.
Extractable/Leachable Studies
Another important part of the validation process is to determine whether there are any substances related to the filter system that can be released into the drug product process stream. Typically, filter cartridges are composed of various thermoplastic polymers that can potentially be extracted or leached into the drug product during the filtration process. A thorough study needs to be completed to characterize this for your final product.
What is the Best Way to Avoid Mistakes in Filter Validation?
Mistakes in the filter validation process can be costly, but there are ways to minimize the risk of errors. If available, review manufacturing history for similar formulations, filter variations, and process guidelines to identify combinations that have been successful in the past and learn about potential difficulties before they arise.
Keep in mind, the ultimate goal of the filter validation is to demonstrate that a given filter will adequately remove bacteria and microorganisms and produce a sterile product. Simulating as much of the production process as possible, as accurately as possible, can help identify red flags before they become costly errors.
The best way to avoid mistakes and pitfalls is to identify the right partner — one with extensive experience in completing filter validation studies across all phases of your development project. Whether you are in early-stage development or looking for a scale-up and manufacturing partner, Particle Sciences has the experience to make your project a success. Contact us to discuss your options and see how Particle Sciences can take your product from concept through commercialization.
Header image courtesy of Pall Corporation.
Authors: