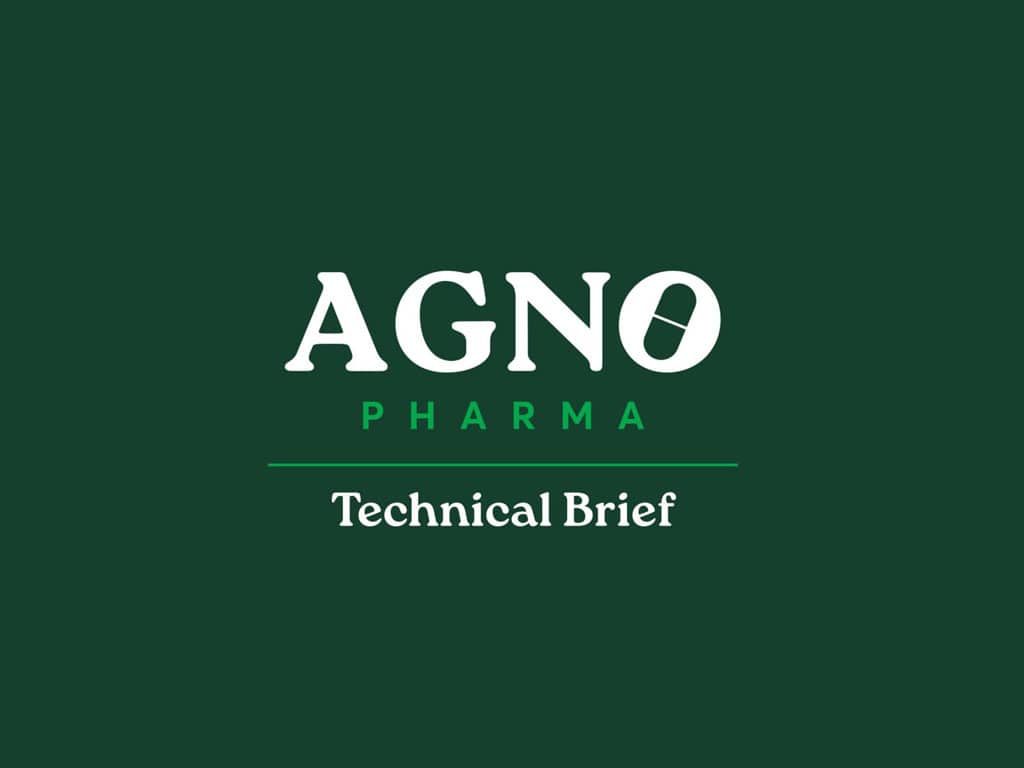
Mechanical Dispersing of Insoluble APIs
Table of Contents
A significant number of products manufactured for pharmaceutical purposes involve, in at least one stage of production, suspensions of liquid or solid particulates, often at high volume fraction. With Active Pharmaceutical Ingredients (APIs) that possess poor aqueous solubility, particle dispersion is a critical quality necessary for maximizing bioavailability and uniformity of a dose.
The state of dispersion of any solid material directly affects suspension properties. As particulate material is added to any liquid medium, its flow becomes increasingly non-Newtonian and, with high particle concentrations, can become thixotropic. These rheological characteristics determine suspension functionality, including film forming, lubricity, and efficacy1,2. Additionally, the profound effect of the dispersion process on the economics and quality of the subsequent product has long been recognized3,4.
Many dry powders start as large particulates and may require size reduction prior to dispersion (see Figure 1) of the powder in a liquid. Fine particulate dry powders always contain agglomerates that require de-agglomeration and stabilization to obtain optimal dispersion.
All suspensions are inherently thermodynamically unstable. Unless properly stabilized through the random motion over time, the particles will aggregate due to the natural and dominant tendency to decrease the large specific surface area and excess surface energy. This tendency becomes increasingly important the smaller the initial particle size (PS) and is especially significant for colloidal-sized particles (less than 1 μm).
Reducing the particle size of an API possessing poor solubility characteristics can be an avenue to substantially increasing the specific surface area and, consequently, the overall bioavailability, regardless of the route of administration. Some routes of administration (ex. intravenous, ocular) necessarily have requirements on acceptable particle size distribution (PSD).
For the above reasons, milling is an important tool available to both the formulator and process engineer. However, it is not a case of one size fits all. Achieving stable, effective and elegant formulations containing particulates is a matter of correct and proper milling. For example, if excessive mechanical energy is used it can easily result in submicron-sized “fines”, especially for crystalline material where fracture can occur along defect crystal planes. Such fines cannot be detected using either image analysis or particle size analysis utilizing Fraunhofer diffraction. Indeed, monitoring the presence of nanoparticles in suspensions that have a broad particle size distribution can be a general problem for current particle sizing instrumentation.
For regulatory approval, the milling technique must be well characterized and reproducible, meaning the product must perform the same every time. A process which provides a poorly controlled PSD, or one that is not adequately characterized, can have great implications on the ultimate performance of the product, i.e., bioavailability. For crystalline materials, milling can also induce changes in crystalline form (polymorphs) or introduce some degree of amorphousness in the particulates. Both events may have practical and regulatory concerns in terms of stability and product performance.
Methods and Equipment
In this section we will restrict ourselves to “top-down” wet milling processes where two operations (size reduction of particles and the breaking down of agglomerates of fine particles) are combined. The former is recognized as a separate unit process in chemical engineering5. Milling may be brought about through four basic processes: impact, shear, extension, and cavitation. However, some would suggest only two: those that pull apart by shear forces and those that comminute by fracture. The degree of turbulence and shear vary considerably with the type of operation and application. The milling equipment and/or its design must be selected with care for both the premix stage (initial wetting of a powder and sometimes de-aeration) and for final dispersion. In all cases, minimum mechanical agitation should be used to avoid unwanted problems.
In general, the smaller the initial PS the more difficult it becomes to reduce the PS further. This is true for both brittle (crystalline) solids and ductile (amorphous or waxy) materials. For many solids, it is not difficult to mill PS to approximately 1 μm. This practical limit is ascribed to the increasing break resistance as the particle size decreases as derived from the smaller size of flaws and defects in smaller particles as compared to those in larger particulates6. Increasingly, however, it is desired to obtain a PS for poorly soluble APIs below 1 μm, known as the colloidal domain7. Sizes in this range begin to assume vastly different, and sometimes unwanted, properties from their larger siblings, one example being Ostwald ripening.
Additionally, the PSD obtained through milling can be broad. As long as it is reproducible and well characterized, however, this may not always be a disadvantage depending on the final requirements of the product. With broad size distributions, higher solid volume fractions can be obtained since smaller particles can be embedded in the voids between the larger particles. Although, in most cases, the desired PSD for pharmaceutical preparations is relatively narrow.
Mechanical dispersion techniques may be broadly characterized as low energy/low shear, low energy/high shear, and high energy/high shear. Some low energy techniques may, in certain cases, provide similar results to high energy techniques, if processed for additional lengths of time. The viscosity of the fluid suspension can have significant impact on the efficiency of particle size reduction; higher viscosities can absorb the energy imparted or impede the movement of the particulates, thus diffusing the impact energy on the particulates.
Most de-agglomeration equipment used to generate shearing forces need only provide sufficient energy to separate the agglomerates. Comminution, however, requires higher energy input to break tightly bound aggregates or to shatter coherent solids.
The generation of high-shear forces requires narrow gaps, high rates of flow, or both. A compounder/extruder mixer used, for example, to incorporate API particulates into plastics to produce material for use in drug-eluting medical devices, functions at low speed but with a loading of high viscosity materials; two kneading arms rotate in opposite directions and at different speeds. They are so shaped that the milling mixture is pressed against the walls of the mill chamber forming a wedge during the kneading operation; the wedge is continuously formed and sheared.
A rotor/stator mill is very commonly used to disperse powders in liquids. This type of mill may be a batch or continuous device in which the rotor turns at high speeds within a labyrinth stator, with a narrow gap between the two. A rotor/stator mixer can normally only operate efficiently with a low viscosity fluid and is limited in the PSD achievable.
Piston/gap homogenizers are used to process suspensions by forcing the particulate/vehicle mixture at high pressure through a small orifice, controlled by some type of valve assembly. These devices function through both cavitation and particle impact. This type of equipment is more commonly used to produce emulsions but can be used in particulate size reduction.
Ultrasonic activators convert conventional 60 Hz line frequency to high (20 kHz) frequency that is fed to an electrostrictive element. This, in turn, converts the signal to mechanical vibrations which induce a shearing action on particles through cavitation of the liquid. Though in existence for many years, ultrasonic processing was not, until relatively recently, scalable to a commercial process. Size reduction by this method can also be limited by the viscosity of the preparation.
Microfluidizer® Processors pump fluid under very high pressure and velocity through precisely defined microchannels within an interaction chamber manufactured from sapphire or diamond. Various designs of interaction chambers are available specific to different applications and desired outcomes (particle reduction, emulsification, etc.). Fine particles with a narrow PSD are produced through a combination of shear, turbulence, impact, and cavitation forces.
A classical method, originally developed in the inks and coatings industry, to de-agglomerate as well as grind particulate material is media milling. The original milling media was flint pebbles, steel shot, or even sand. It is now available as very high purity, dense, non-porous ceramic, as well as polymeric materials, so as to meet the strict requirements of pharmaceutical usage. The simplest method of media milling is roller milling. Media and fluid are loaded into a jar or vessel which is then rotated on a shaft or by rollers; the “impacts” are driven by gravity. The speed of rotation, the amount, and size of the grinding media and the amount of fluid loading are all critical parameters that control the efficiency of the milling process. The impact depends on attaining a cascading motion and hence the media must be dense (i.e., zirconia, ρ ≈ 6 and tungsten carbide, ρ ≈ 16). However, even with very dense media, a limit is reached as its size decreases and milling fluid viscosity increases. Stirred media mills can use smaller grinding media resulting in a finer grind. Here the grinding media is moved by the rotation of some type of impellor rather than relying on the force of gravity (thus enabling the use of low-density polymeric media). In addition to impact, this motion generates shear fields leading to more efficient power consumption and shorter grinding times. Stirred media mills may be simple, like a pegged impellor immersed into a slurry of fluid and media, or quite complicated, such as high speed/high-energy, continuous flow media mills with cooling and recirculation capabilities.
Jet mill micronization is a dry process in which particles are introduced into a stream of high pressure gas (the “fluid”) and then injected into a chamber, creating a vortex of the fluidized gas and particulate material. Within the chamber the particulates are subjected to additional gas flow from high-speed jet nozzles that project particle-particle collisions at high kinetic energies. As particulates are broken down by these collisions, they are classified by centrifugal force and discharged by the mill. As this method generates very little heat, owing to the large volume of gas moving through the system, it is particularly well-suited for materials having low melting points or temperature sensitivity.
References
- R. Eirich (ed), Rheology, Theory and Applications, Vols I-V, Academic Press, New York (1956).
- Goodwin and R. Hughes, Rheology for Chemists – An Introduction, RSC Publications, Cambridge (2000).
- K. Daniel, Natl. Paint, Varn. Lacquer Assoc. Sci. Sect. Circ., No. 744 (1950).
- Guggenheim, Off. Dig., 30 No. 402, 729 (1958).
- Bernotat and K. Schöert, in Ullmann’s Encyclopedia of Indus- trial Chemistry, eds. W. Gerhartz,
- Elvers et al, Fifth Edition, Vol. B2, Wiley-VCH Verlag, Weinheim (1986).
- N. Stein, The Preparation of Dispersions in Liquids, Marcel Dekker, New York (1996)
- H. Everett, Basic Principles of Colloid Science, RSC Publications, London (1988).